라이프치히 공장 세 종류 번갈아가며 이동
섀시·파워트레인 결합 ‘메리지’ 공정 백미
사람대신 로봇·나사조립 설비 작업 ‘척척’
주펜하우젠 공장은 전기차 라인 별도 운영
고객 맞춤형 수작업·대량 양산 공장 공존
‘캐즘’ 넘어 수요 늘 땐 유연한 대응 전략
“하나의 팀. 세 개의 구동장치. 꿈을 현실로 만듭니다.”
13일(현지시간) 찾은 독일 라이프치히의 포르셰 공장 입구에는 이 같은 문구가 적혀 있었다. 내연기관차, 하이브리드차(HEV), 순수전기차를 모두 하나의 라인에서 혼류생산하며 포르셰의 정체성을 불어넣는 이 공장의 특징을 나타낸 것이다.
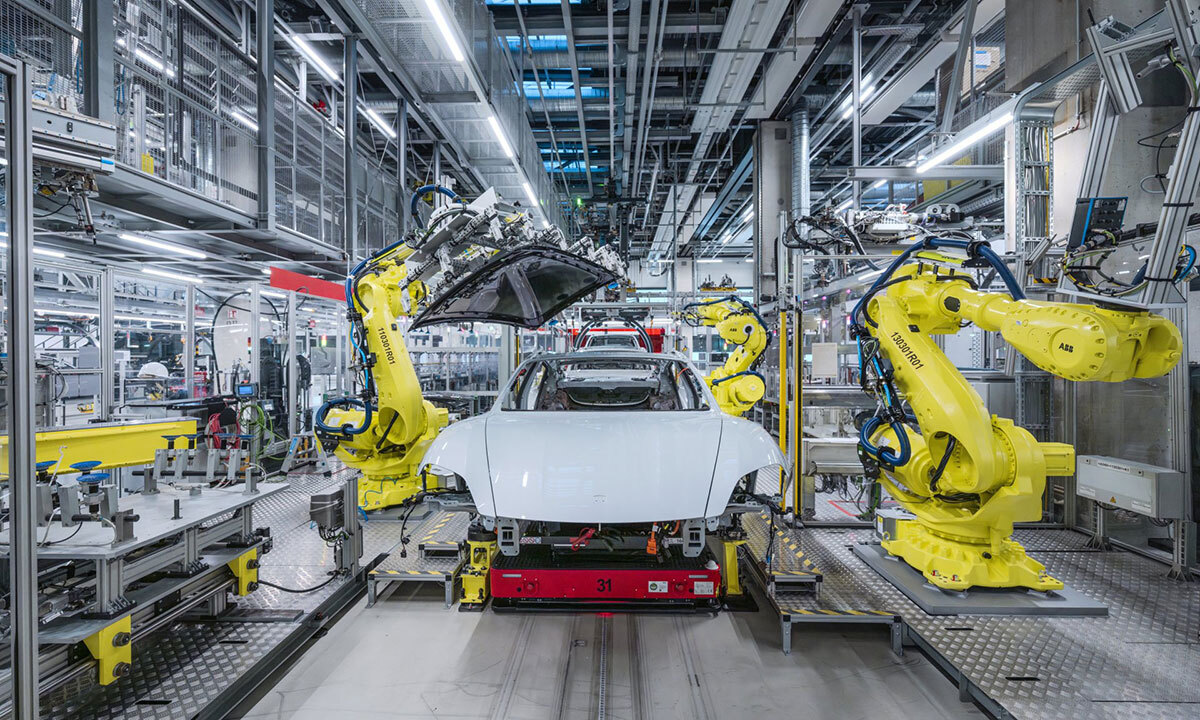
2002년 준공과 함께 포르셰의 21세기를 연 라이프치히 공장은 포르셰의 전동화 거점이자 변화를 상징하는 곳이다. 2010년부터 첫 하이브리드 모델인 카이엔 S 하이브리드가 이곳에서 생산됐고, 현재 여러 파워트레인을 유연하게 생산할 수 있는 시스템이 구축됐다. 실제로 조립라인에 들어서자 내연기관차 마칸과 전기차 마칸 일렉트릭, 내연기관차와 하이브리드차 두 가지의 파나메라가 번갈아가며 이동하고 있었다. 직원들은 차 한 대당 한 명에서 많게는 네 명이 함께 부품이 연결된 기계 의자에 앉거나 서서 하부를 조립하는 데 여념이 없었다.
자동차 조립 공정의 핵심으로 일컬어지는 ‘메리지’ 공정은 섀시와 파워트레인을 결합하는 것으로, 복잡한 혼류생산 기술의 결정체다. 리프트에 매달려 있던 섀시가 바닥의 파워트레인 위에 포개진 뒤 로봇팔이 바쁘게 움직이며 나사를 박아 고정했다. 하나의 조립 라인에 설치된 로봇 6대와 자동 나사조립 설비 18대가 토크와 각도를 자동으로 제어해 차종별로 다른 나사의 수와 위치를 점검해 작업하는 방식이다.
포르셰의 라이프치히 공장이 완성형에 가깝다면 슈투트가르트의 주펜하우젠 공장은 포르셰의 전통을 기반으로 전동화 변화가 한창 진행 중인 곳이다. 이곳에서는 1950년대부터 911 등 포르셰를 대표하는 다양한 스포츠카가 생산됐고 2019년 포르셰의 첫 전기 스포츠카 타이칸 생산이 시작했다.
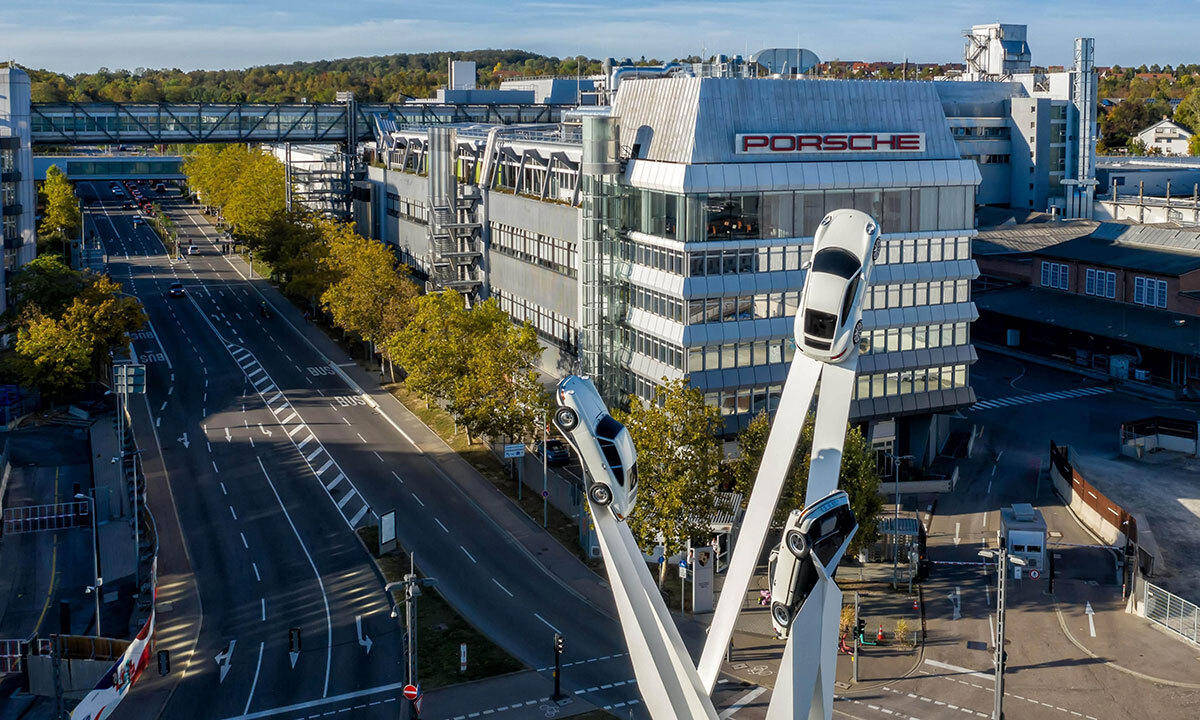
16일 찾은 주펜하우젠 공장은 오래된 붉은 벽돌 공장과 신축 고층 건물이 섞여 있었다. 맞춤형 제작을 하는 포르셰 익스클루시브 매뉴팩처 등 집중 수작업장과 대량생산 공장도 공존하고 있었다. 이 가운데 타이칸 조립공장 내부에 들어서니 깔끔하고 쾌적한 현대식 시설이 눈에 들어왔다.
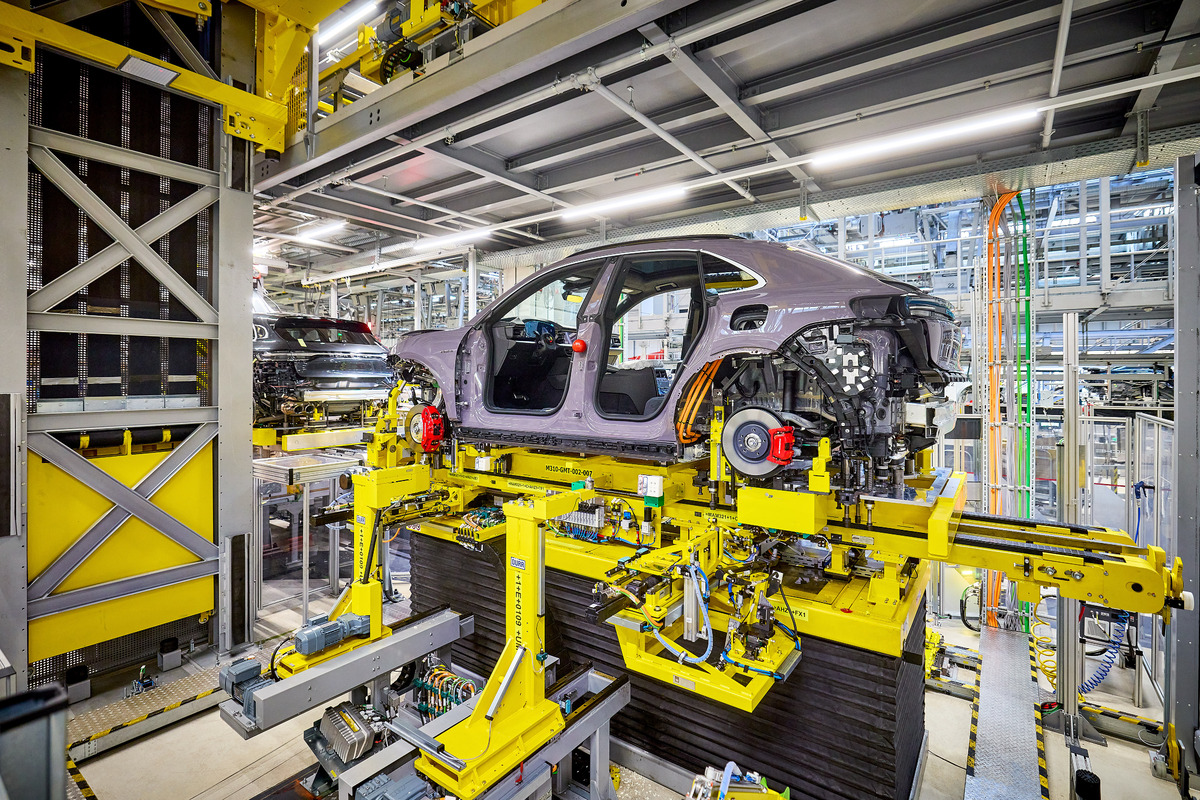
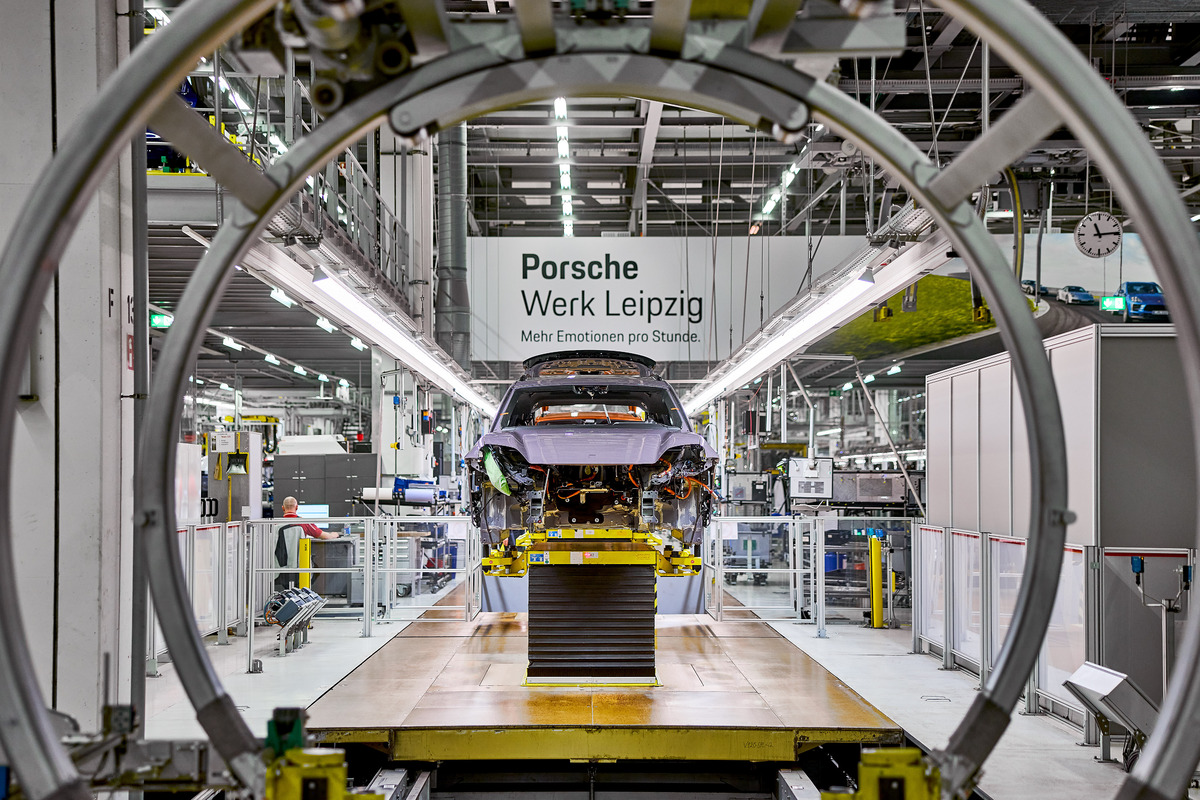
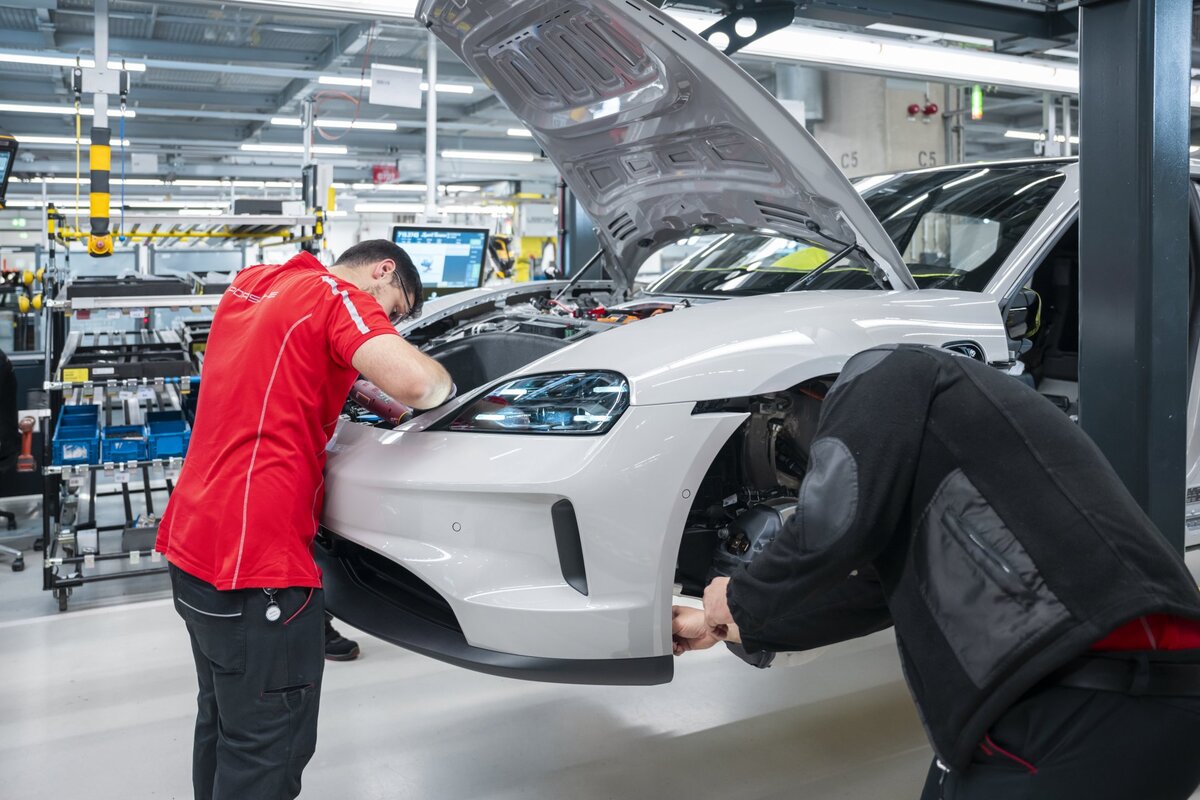
공장 내부는 차량 이동보다는 작업의 효율성과 집중도에 초점을 맞춰 입체적으로 공간을 활용하는 모습이었다. 생산 차량들은 전통적인 컨베이어벨트 대신 천장의 레일을 따라 이동하는 기계에 매달려 작업에 따라 높낮이와 회전 각도가 수시로 바뀌었다. 바닥에서는 자율주행로봇 여러 대가 쉴 새 없이 부품을 실어날랐다.
주펜하우젠 공장은 전기차 라인이 별도로 운영되며 전기차 수요가 늘어날 경우 향후 911 공장이 전기차 생산에 활용될 가능성도 있다. 다만 글로벌 전기차 시장의 수요 정체와 경쟁 심화 등으로 포르셰도 중국 시장 등에서 부진을 겪고 있다. ‘포르셰표 전기차’로 시장에 자리매김하는 것과 탄력적인 전동화 전략을 세우는 것이 그 어느 때보다 중요한 시점이다.
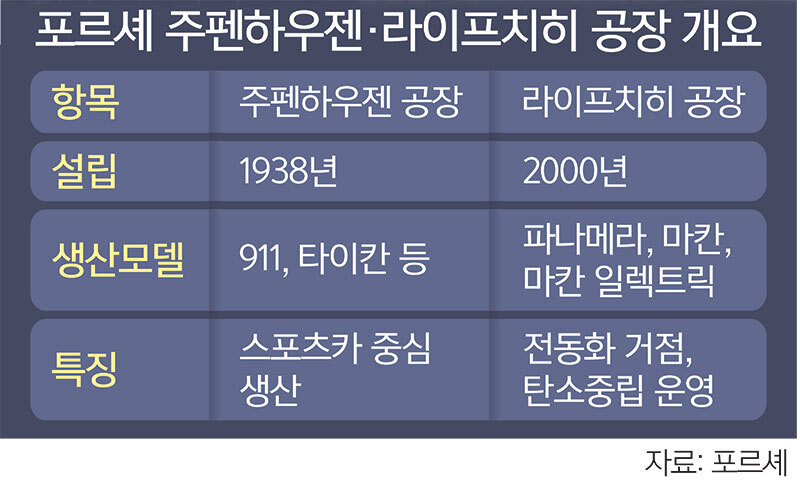
주펜하우젠 공장을 책임지고 있는 젠스 브뤼커 포르셰 사장은 “주펜하우젠 공장은 기술적인 경쟁력과 장인정신도 갖고 있어 전체적인 라인 안에서도 고객마다 맞춤 생산이 가능하다”며 “앞으로 내연기관차나 전기차 수요에 따라 대응할 수 있도록 대비하며 유연하게 공장을 운영하고 있다”고 말했다.
[ⓒ 세계일보 & Segye.com, 무단전재 및 재배포 금지]