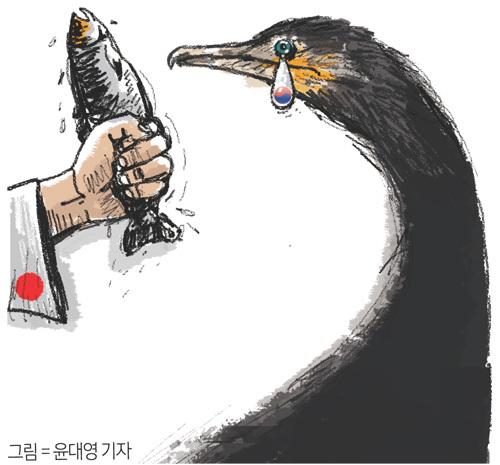
일본의 대한(對韓) 반도체·디스플레이 핵심소재 수출규제로 한국 경제의 허점이 적나라하게 드러났다. 세계 소재·부품 시장 6위, 메모리 반도체 세계 1위의 위상에도 불구하고 우리 산업계는 일본이 중간재 수입을 막으면 타격을 받을 수밖에 없다는 사실이 새삼 확인된 것이다. 특히 주력산업의 소재·부품은 대일 의존도가 갈수록 심화되고 대일 무역수지 적자폭도 커지고 있는 것으로 나타났다.
28일 한국기계산업진흥회에 따르면 2017년 소재·부품의 대(對)일본 무역적자 160억달러 가운데 70%가 전기·전자(58억달러)와 화학제품(54억달러) 부문에서 발생했다.
특히 전체 소재·부품의 대일 무역수지 적자가 2010년 이후 감소 추세인데도 전기·전자는 2010년 41억5000만달러에서 2017년 57억8000만달러로 적자폭이 확대됐다. 화학제품은 같은 기간 26억6000만달러에서 54억달러으로 적자가 2배이상 늘었다. 반도체와 디스플레이에 이어 2차전지와 미래자동차 등이 일본의 다음번 수출규제 타깃이 될 것이라는 분석이 나오는 이유다. 같은 기간 정밀기기(7억4000만달러→ 16억1000만달러), 일반기계(14억4000만달러→ 17억2000만달러), 비금속광물(2억7000만달러→ 4억6000만달러)의 소재·부품 역시 대일 무역 적자 규모가 커졌다.
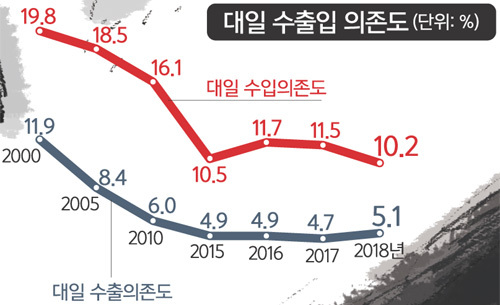
삼성전자와 SK하이닉스가 세계 메모리 반도체 시장의 60%를 점유하고 있지만, 소재와 생산장비의 국산화 비율은 절반에도 미치지 못하는 것으로 알려졌다. 스마트폰의 전자나침반이나 터치스크린, 자율주행차의 핵심 부품인 광학렌즈, 공장자동화의 필수 부품인 공작기계 등의 원천기술도 일본이 보유하고 있다. 일례로 삼성전자 갤럭시폰의 곡선형 모서리는 일본의 산업용 장비제조사 화낙(FANUC)의 절삭기술로 만들고, 갤럭시노트 시리즈 비장의 무기인 전자펜 ‘S펜’은 일본 와콤이 원천기술을 갖고 있다. 디스플레이 장비의 경우 반도체에 비해 상대적으로 국산화율이 높지만, 역시 일부는 국산화가 어렵고 독과점 품목의 경우 공장 건설에 차질을 빚을 수 있다. 올레드(OLED·유기발광다이오드) 패턴 형성, 기타 건식각기 등은 일본에 100% 의존하고 있다.
일본의 경제평론가인 고무로 나오키는 한국 경제의 이 같은 소재·부품 대일본 의존을 “목줄(부품·소재 산업)에 묶인 채 잡아먹은 물고기(완제품)를 어부(일본)에게 바치는 ‘가마우지 경제’”라고 조롱했다.
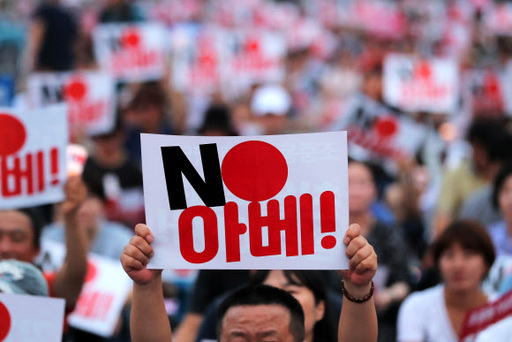
이처럼 주력산업이 과도하게 일본에 의존하게 된 것은 내수가 작은 우리나라의 태생적 수출구조에서 기인하는 측면이 크다.
정은미 산업연구원 성장동력산업연구본부장은 “정밀 소재나 부품을 개발하기 위해서는 많은 시간과 경험이 필요한데 선택과 집중을 통해 선진국 추격형으로 성장한 우리는 그런 축적의 시간이 없었다”며 “당시 일본이 필요한 소재와 부품을 공급해주니 (개발할) 유인이 없었던 것도 사실”이라고 말했다. 수출주도 압축성장에 최적화된 경제산업구조를 가진 한국은 국제분업에서 빠른 시일 내에 경쟁력을 갖출 수 있는 조립가공에 집중하다 보니 원천기술을 개발할 여유도, 유인도 부족했다는 것이다.
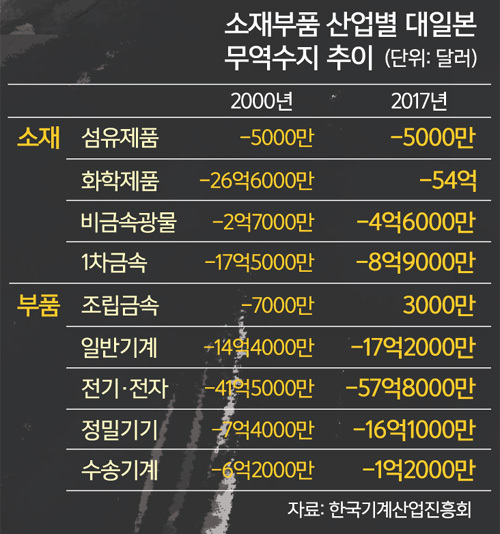
2000년 초반 선진국들이 첨단산업으로 산업구조를 고도화해 갈 때 기회를 놓친 것도 소재부품 산업 부진의 원인으로 꼽힌다. 선진국을 따라 첨단 고기능 산업에 뛰어들어야 할 시기에 싸게 빨리 만드는 중국시장이 열리고, 이어 아시아 시장까지 확장되자 우리 산업계는 첨단화, 고도화가 아닌 대량 양산체제를 택했다.
제조업계의 한 관계자는 “우리나라는 강소기업을 키울 만한 시간도, 시스템도, 인내심도 없었고 국내 중소기업이 기술혁신 해서 어렵게 제품을 만들어도 일본이 금세 가격을 낮춰 들어오면 속수무책이었다”고 말했다.
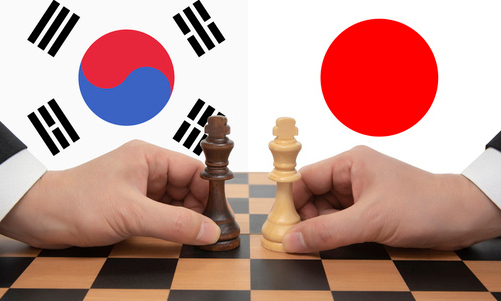
◆바이오 소재 3년, 전기·전자 1.3년 뒤처져
한국 산업계의 대일 수입 의존도는 다소 개선됐지만 핵심 소재·부품 분야의 기술력은 여전히 일본을 따라잡기 힘든 수준인 것으로 나타났다. 특히 한·일 중소기업의 기술 격차가 크다.
28일 통계청 국가통계포털의 ‘일본 대비 기술격차’ 자료에 따르면 2017년 기준 한국의 연 매출액 5억∼1500억원인 중소 제조업 기술 격차는 평균 -1.8년으로 집계됐다. 기술 격차는 현장에서 느끼는 한국 기업의 핵심기술과 일본 기술 수준의 체감 격차 연수로, 업체별로 일본에 몇 년 앞서 있는지 혹은 뒤처져 있는지 설문한 다음 평균을 냈다.
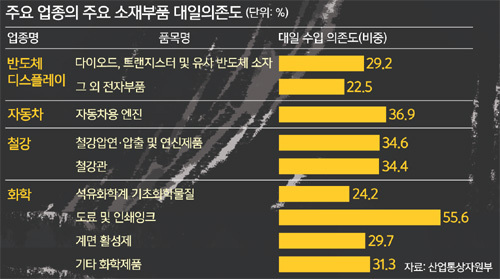
조사 대상이었던 5만1373개 기업 중 일본보다 기술이 앞선다고 응답한 업체는 6.6%에 그쳤다. 16.5%가 일본 업체와 동일한 기술 수준이라고 답했고, 나머지 76.9%의 경우 일본에 많게는 4년 이상 기술이 뒤처져 있다고 응답했다. 평균 기술 격차가 일본보다 앞선 분야는 72개 업종 중 반도체장비 분야가 유일했다. 반도체장비는 일본에 비해 평균 0.4년 빠른 것으로 조사됐으며, 일본보다 4년 이상 기술이 앞섰다고 응답한 업체도 5.4%였다. 중소 제조업 중에서 기술 평균 격차가 가장 큰 분야는 대기·폐기물 업종으로 -3.1년이었다.
소재·부품 분야는 대부분 일본에 크게 뒤져 있었다. 고분자 재료·광전자 소재·바이오 소재가 각각 -3년, 기계·구조 소재 -2.9년, 금속재료 -2.5년, 정밀화학 -2.3년, 요소부품 -2년, 섬유재료 -1.7년, 전기·전자제품 -1.3년 등이었다.
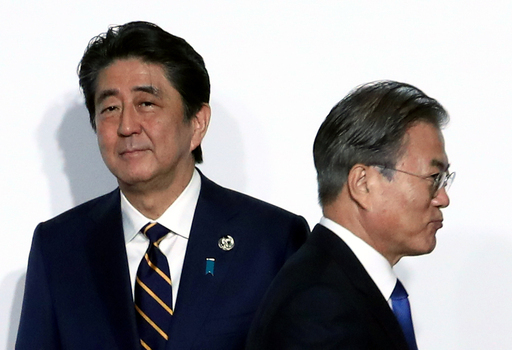
한국경제를 이끌고 있는 반도체·디스플레이 등 주요 산업이 일본의 소재·부품에 의존해있는 셈이다. 이번에 일본이 수출을 규제한 세 가지 품목(에칭가스, 플로오린 폴리이미드, 포토 리지스트) 등이 대표적이다.
탄소섬유 역시 일본 도레이, 도호, 미쓰비시레이온이 시장을 선도하고 있으며 세계 시장 점유율은 66%에 달한다. 탄소섬유는 철보다 4배 가볍고 10배 강한 초경량·고강도 소재로, 수소차에 들어가는 수소연료탱크의 핵심 소재다. 일본 언론들은 탄소섬유와 전기차 핵심부품인 배터리, 정밀공작기계 등이 추후 수출규제 대상으로 포함될 것으로 전망했다.
전기차배터리 중에서 파우치형 배터리의 포장재 역할을 하는 ‘파우치필름’의 경우 일본의 세계 시장 점유율이 85%에 달한다. 국내에서 SK이노베이션과 LG화학 등이 파우치형 배터리를 생산하고 있으며, 파우치필름은 전량을 일본에 의존하고 있다. 최근 이들 회사는 국내 업체와 접촉해 파우치필름 국산화를 타진하는 것으로 알려졌다. 정밀공작기계도 국내 제조사들이 다양한 분야에서 일본산을 사용 중이다. 특히 수치제어기계(CNC) 로봇 감속기 등 정밀 부품에서 일본 의존도가 높은 것으로 나타났다.
김수미·이우중 기자 leolo@segye.com
[ⓒ 세계일보 & Segye.com, 무단전재 및 재배포 금지]